Футеровка индукционных печей тигельных (см. рис. 1) состоит из 6 основных элементов: тигля, подины, воротника, сливного носка, крышки печи и обмазки индуктора. Основным элементом футеровки является тигель, поэтому правильный выбор огнеупорного материала для тигля в основном обеспечивает надежность работы печи и ее технико-экономические показатели, заложенные в конструктивном решении печи.
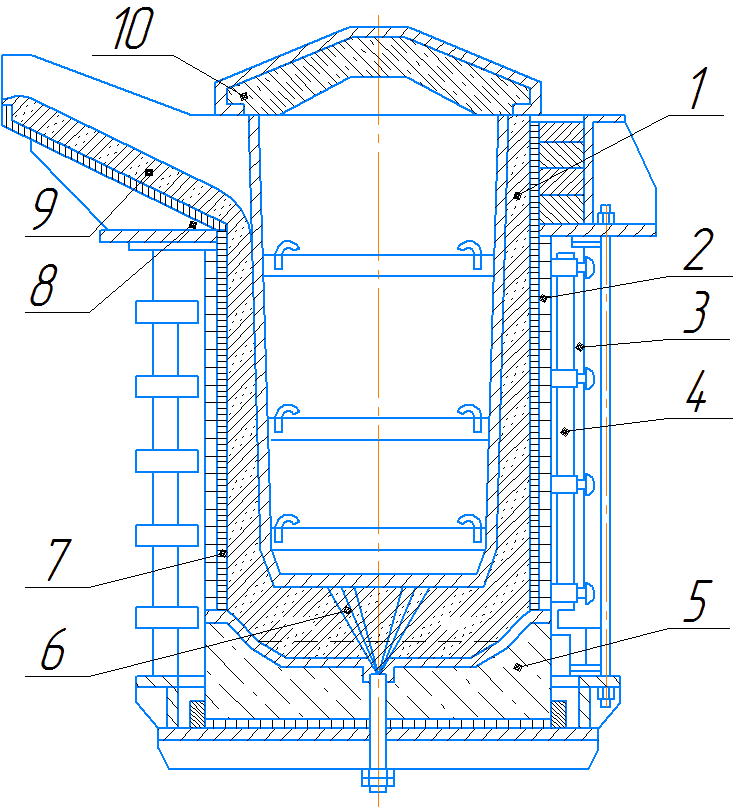
Рис.1. Футеровка тигельной индукционной печи:
1 — огнеупорный тигель; 2 — индуктор; 3 — стальной корпус печи; 4 — магнитопровод; 5 — подина; 6 — сигнализатор износа (проедания) тигля; 7 — огнеупорное покрытие (обмазка); 8 — воротник; 9 — сливной носок; 10 — крышка.
Выбор вида футеровки индукционной тигельной печи
Тигель индукционной печи может быть выполнен четырьмя различными методами: выемным (в печах малой емкости), набивным, в виде кладки из огнеупорных изделий и комбинированным, сочетающим кирпичную кладку рабочего слоя и набивку буферного слоя между индуктором и кладкой. При образовании трещин в швах кирпичной кладки буферный слой задерживает металл от прохода его к индуктору.
Каждый из перечисленных методов футеровки может быть выполнен из следующих видов огнеупорных материалов: кварцитового (кислого) SiO2; магнезитового (основного) — МgO; шпинельного — МgO + Al2O3 или MgO + Cr2O3; корундового — Al2O3; муллитового — ЗAl2O3 · 2SiO2; муллитокорундового — Al2O3 ≥ 72 %; шамотного; цирконового — Zr2 · SiO2; циркониевого — ZrO2; шамотнографитового; графитового и т. п. Все эти виды футеровки могут иметь несколько вариантов по зерновому составу и содержанию (массовые доли) различных компонентов и добавок (табл. 1), улучшающих спекание, уменьшающих объемные изменения при обжиге и увеличивающие стойкость футеровки к различным видам выплавляемых металлов и шлаков.
Таблица 1. Данные для выбора вида футеровки индукционных тигельных печей и миксеров для чугуна и стали
№ п.п. | Типы печей и элементы футеровки | Марки выплавляемых металлов | Состав оптимальной футеровки | Стойкость футеровки, мес | Заменители менее дефицитные, уменьшающие стойкость футеровки |
1 | Тигель печи промышленной частоты для чугуна ёмкостью 6-60 т | Чугун марок: СЧ15-32; СЧ50-90; СЧ21-40; СЧ28-48; ВЧ 45-5 | Первоуральский кварцит ПКМИ-97,5 с борной кислотой 1,5% (ГОСТ 9656-75) или с борным ангидридом 1% | 1-4 | Овручский молотый кварцит ПКМ-97 с добавкой 10-12% кварца молотого пылевидного марки А (маршалита) ГОСТ 9077-82 |
2 | Тигель печи промышленной частоты для чугуна и высокоуглеродистой стали ёмкостью 1-10 т | ВЧ 50-2; ВЧ 45-2 | Дистенсиллиманит — 60%, электрокорунд №200 — 40% | 1-2 | Овручский молотый кварцит ПКМ-97 с добавкой 12-15% кварца молотого пылевидного марки А |
3 | Тигель печи для чугуна и стали ёмкостью 0,1-6 т | Чугун всех марок, сталь углеродистая, низколегированная | Масса МЛ-2 | 3-8 | Местные кварцевые пески с добавкой 10-20% кварца пылевидного марки А |
4 | Выравнивающая обмазка, наносимая на индуктор тигельных печей для плавки чугуна и углеродистых сталей | Кварцит от 0 до 1 мм — 70%, высокоглинозёмистый цемент ВЦ-75 | 6-12 | Смесь муллитокорундовая с цементом для огнеупорных бетонов марки СМКЦ | |
5 | Нижнее и верхнее бетонное кольцо для печей ёмкостью более 6 т | Заполнитель ЗМКР (ГОСТ 23037-78) класс 4 — 70%, высокоглинозёмистый цемент ВЦ-70; ВЦ-75 или алюминат кальция технический — 30% | 24-36 | Огнеупорная смесь алюмосиликатная бетонная на высокоглинозёмистом цементе марок СМКРВЦ-45; СШВЦ-40 или СШЦ-5 | |
6 | Сливной носок, воротник и крышка печи | Масса муллитокорундовая МК-80 или масса корундовая гидравлическая МКН-94 ТУ 14-8-359-80 | 6-12 | Масса марки МЛ-2 или МЛ-3 | |
7 | Тигель печи для углеродистой стали ёмкостью до 6 т | Сталь инструментальная, углеродистая, хромоникелевая и др. низколегированные марки | Кислая — кварцит ПКМИ-97,5 — 89%, борная кислота 1,5% или борный ангидрид — 1%; кварц пылевидный марки А ГОСТ 9077-82 — 10%; нейтральная масса МК-80 или МК-90 | 0,5-1 | Овручский кварцит, борный ангидрид 1%, кварц пылевидный марки А — 15%, масса МЛ-2 или МЛ-3 |
8 | Тигель печи для высоколегированной стали | Высоко легированные и марганцевые стали | Магнезитовый порошок марок ПМЭ-88, ПМИ-88, ПМИ-90 фракции 4-2 мм — 10%, фракции 2-1 мм — 14%, менее 1 мм — 14%; магнезитохромитовый порошок фракции 4-2 мм — 10%, фракции 2-1 мм — 15%, менее 1 мм — 35%; плавиковый шпат — 2% | 0,3-0,5 | Порошок магнезитовый (периклазовый) марки ПМ |
9 | Тигель ёмкостью до 3 т для открытых и вакуумных печей | Высоколегированные и прецизионные сплавы | Порошок из плавленного магнезита для индукционных печей марки ПППВИ и ПППОИ-93 — II; III; IV; V; VI в соотношении 1:2:2:2:3 — 83%; электрокорунд №6 — 12-15%; плавиковый шпат или борный ангидрид — до 1,5% | 0,5-1 | — |
10 | Тигель печи для стали и никеля ёмкостью 16 т и более | Сталь всех марок и никель | Кирпич периклазовый клиновой марок Му 91-11 (12), Му 91-7 и прямой Му 91-1 ГОСТ 4689-74, буферный слой из магнезита металлургического МПМП-86 | 2-4 | Изделия корундовые плотные клиновые для индукционных печей ТУ 14-8-187-75 (Al2O3 ≥ 90%, P2O5 ≥ 1%) |
11 | Металлостойкая обмазка — для индукторов печей для стали и др. сплавов чёрных и цветных металлов | 1-й слой: кварцит молотый марки ПКМИ-97,5 от 0 до 1 мм или ПКМ — 75%; цемент ВЦ-75 — 25%; 2-й слой: асбестовая ткань АТ-2 или АТ-7 ГОСТ 6102-78; 3-й слой: порошок периклазовый спечённый молотый марки МПМП-86 — 88%, полифосфат натрия технический ГОСТ 20291-90 — 12% | 12-24 | 1-й слой: смесь порошков марки СВШЦ-3; 2-й слой: асбестовая ткань АТ-2 или АТ-7; 3-й слой: порошок периклазовый марки ПППОИ-90-1 — 88%, полифосфат натрия 12% |
Для оптимального решения в выборе того или иного вида огнеупорных материалов необходимо учитывать конкретные службы футеровки тигля, вид выплавляемого металла, а также стоимость и дефицитность огнеупора. Как показала практика, основным фактором при выборе футеровки является срок ее службы, обеспечивающих надежную работу печи в данных условиях. Технически обоснованный выбор вида и метода футеровки должен обеспечивать следующие требования:
- выплавку металла высокого качества;
- наибольшую продолжительность межремонтного цикла работы печи;
- надежность и безопасность работы обслуживающего персонала;
- стабильность проведения металлургического процесса;
- более высокие экономические показатели;
- недефицитность применимых материалов;
- минимальное загрязнение окружающей среды отходами футеровки.
Футеровка оказывает существенное влияние на химическую чистоту и на физико-механические свойства выплавляемого металла, например, на пластичность стали при обычных и высоких температурах, структуру, усталостную прочность, длительную жаропрочность, ползучесть, коррозийную стойкость и др. Наряду с полезными, вводимыми в ванну (тигель) легирующими добавками и раскислителями в процессе плавки образуются нежелательные примеси, которые вредно отражаются на качестве металла. Эти смеси обычно попадают в металл в виде неметаллических включений, образующихся в результате взаимодействия с поверхностью футеровки, а также из шихты или в виде оксидов металлов, получающихся при окислении расплава кислородом воздуха, вовлекаемым при движении расплавленного металла или при окислении раскислителей.
Наиболее распространенными нежелательными примесями являются кислород и его соединения в виде простых и сложных оксидов (SiO2; Al2O3; FeO; Fe2O3; Cr2O3; MgO; ZrO2; FeCr2O4; FeAl2O4; MgAl2O4), силикатов; алюмосиликатов и др. Уменьшение содержания нежелательных примесей (в том числе и неметаллических включений) — одна из основных проблем качественной металлургии [12].
Сталь, выплавляемая в основных тиглях, обладает более высокими прочностными и пластическими свойствами, чем сталь, выплавляемая в кислом тигле. Причиной этому является образование кремнекислородных включений в результате взаимодействия металла с кислой футеровкой. Включения, богатые кремнеземом, хорошо смачиваются жидким металлом, трудно удаляются из него, так как имеют пониженное поверхностное натяжение, а включения оксида магния, корунда и соединения типа шпинелей (R0 · Al2O3) плохо смачиваются металлом и быстрее удаляются из него. По понижению межфазового натяжения материалы включений располагаются в следующем порядке: α-Al2O3 (корунд); MgO · Cr2O3; MgO · Al2O3; FeO · Al2O3; алюмосиликаты и SiO2. Отсюда следует, что для получения металла с меньшим содержанием неметаллических включений наиболее эффективными являются футеровки шпинельного типа (RO · Al2O3 и RO · Cr2O3), а также химически чистые основные огнеупорные материалы с минимальным содержанием кремнезема.
Для плавки специальных сталей (12Х18Н10Т и др.) стойкой (19-25 плавок) в тиглях емкостью 8 т [13] является масса, состоящая из обожженного периклазового порошка фракции 4-2 мм (с массовой долей MgO ≥ 88 %), периклазошпинелидного порошка фракции 2-0 мм и плавленого периклаза фракции 4-0 мм (MgO ≥ 93 %) в соотношении 3:3:1. Высокую расплавоустойчивость массы обеспечивает периклаз, являющийся наиболее стойким к расплаву металлов и шлака, а также наличие периклазошпинелидного порошка, обладающего плотной структурой повышенной термостойкостью вследствие присутствия хромита в тонкомолотом состоянии.
При выборе вида футеровки необходимо учитывать склонность некоторых металлов к обменной реакции окисления с оксидами, входящими в состав футеровочных масс. Это свойство зависит от теплоты образования оксидов, которая для наиболее распространенных огнеупоров является следующей (кДж/моль) : MgO — 608, SiO2 — 435, Al2O3 — 562, Cr2O3 — 381, ZrO2 — 540,1, Fe2O3 — 276,1, ТiO2 — 456.
Из приведенных данных следует, например, что алюминий можно плавить в тиглях из оксидов магния и алюминия. Кислая футеровка будет восстанавливаться алюминием и его сплавами, поэтому кварцит не может быть применен в индукционных печах для плавки алюминиевых сплавов.
Реакции, протекающие на контакте металл—огнеупор, имеют большое значение как для правильного выбора вида футеровки печи, так и с точки зрения качества выплавляемого металла. Склонность расплавленных металлов и сплавов к окислению повышается в следующей последовательности: никель, нихром, железо, хром, кремний, титан, цирконий, алюминий, магний, а склонность огнеупоров к восстановлению уменьшается в ряду: Cr2O3; SiO2; TiO2; ZrO2; Al2O3; MgO; MgAl2O4. Контактная реакция между расплавом стали и кислой футеровкой может быть представлена следующим уравнением:
2Fe + SiO2 + O2 = 2Fe2+ + Si044- → (Fe2 · Si04)
Контактные реакции взаимодействия происходят главным образом на поверхности рабочего слоя в системе жидкий металл—твердая футеpoвка с участием вовлеченного в металл кислорода воздуха. Прочность связи поверхностного слоя (фаялита) с последующими слоями футеровки ослабляется с увеличением его толщины. Затем слой фаялита уносится движущимся расплавом и всплывает наверх в виде шлака, так как его удельная масса (4,0-4,35) меньше удельной массы стали. Температура плавления фаялита 1200 °C значительно ниже температуры плавления стали и чугуна, поэтому при плавке черных металлов в кварцитовом тигле нет необходимости наводить шлаки.
Защитный шлаковый покров предотвращает окисление металла кислородом воздуха, обеспечивает его рафинирование, уменьшает содержание в нем нежелательных примесей и неметаллических включений. При плавке металла в основных огнеупорных тиглях шлаки почти не образуются, поэтому в основной тигель дают добавки, образующие шлак: плавиковый шпат, буру, известь, магнезит, известковое стекло, кварцевый песок, оксид алюминия, порошок шамота, различные соли и др. Эти материалы иногда перед началом плавки помещают на дно тигля. По мере расплавления они нагреваются, плавятся и, будучи легче металла, всплывают на поверхность, закрывая металл.
При плавке черных металлов износ футеровки чаще всего происходит равномерно в виде размывания в соответствии с 2-контурным движением металла в крупных печах промышленной частоты. В этом случае износ зависит от агрессивности различных марок металла. Ориентировочно по степени агрессивности черные металлы можно расположить в нижеследующем порядке.
При плавке стали в высокочастотных печах движение металла менее интенсивное, износ футеровки более равномерный и при прочих равных условиях стойкость футеровки выше, чем в печах промышленной частоты (рис. 2).
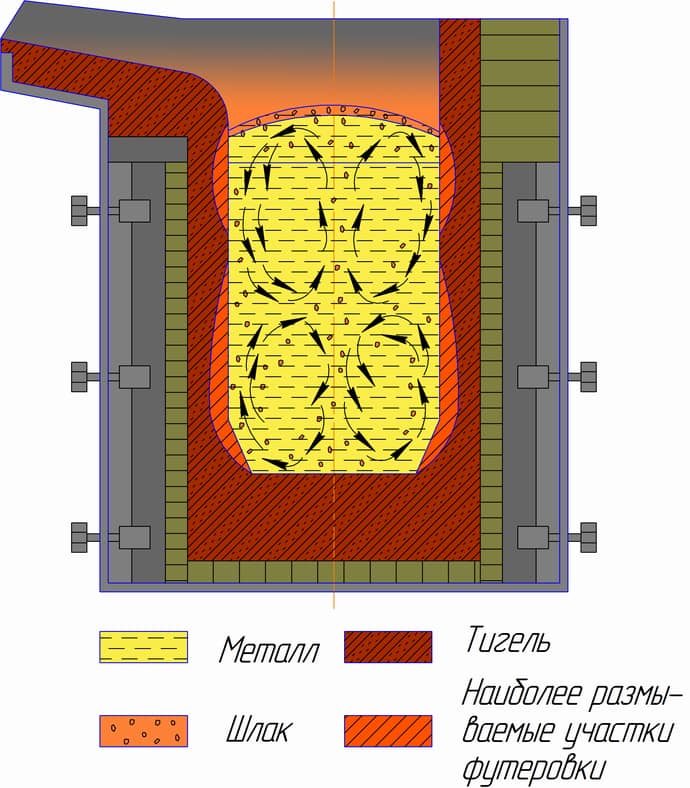
Кислую футеровку обычно применяют в печах любой емкости (до 60 т) для плавки чугуна, углеродистых, кремнистых и других сталей с перегревом металла до температуры 1450-1550 °C. Однако кислая футеровка не может быть использована при выплавке многих марок качественных сталей и сплавов, в которых строго лимитируется содержание углерода, кремния, фосфора, серы, неметаллических включений. Выгорание этих примесей значительно быстрее происходит в основной футеровке. Оксид кальция (известь), добавляемый для рафинирования стали от кремния, серы и фосфора, взаимодействует с кислой футеровкой и, не успевая соединиться с серой и фосфором металла, уходит в шлак. Кремний же частично переходит из материала кислой футеровки в сталь. Жаропрочные и тугоплавкие сплавы опасно плавить в печах с кислой футеровкой еще и потому, что температура плавления и перегрева этих металлов близка к температуре плавления кварцитов.
Стойкость кислой футеровки зависит от вида выплавляемого металла и колеблется в широких пределах от 10 до 300 плавок. При плавке чугуна стойкость футеровки из первоуральского кварцита ПКМИ-97,5 достигает 4 мес. Высокая стойкость может быть достигнута только при тщательном уходе за тиглем и ремонтах изношенной футеровки. На Горьковском автозаводе стойкость тигельных печей емкостью 10-12 т стабильно составляет 3-4 мес или 300 плавок. Плавку ведут без наведения шлаков, чугун полностью не сливают. При применении кислой футеровки в шлак нельзя добавлять плавиковый шпат CaF2 и буру Na2B4O7, так как в этом случае стойкость футеровки резко падает (до 2-3 плавок). При плавке высокомарганцевых сталей стойкость кислой футеровки также очень низка. Однако в практике футеровки тигельных индукционных печей кислая футеровка применяется чаще, чем другие виды футеровок. Причины этому следующие: а) дешевизна кварцита; б) недефицитность футеровки; в) полиморфные превращения кварца обеспечивают безусадочность рабочего слоя и плотность неспеченного буферного слоя; г) нет необходимости в наведении шлаков; д) мала вероятность образования сквозных усадочных трещин, что обеспечивает надежность работы печи; е) стабильный достаточно высокий срок службы тигля.
Учитывая указанные преимущества, высококачественную кварцитную футеровку (из шведских молотых кварцитов) с борным ангидридом в зарубежной практике применяют также для попеременной выплавки чугунов и легированных сталей в крупных тигельных индукционных печах. На одном из литейных заводов фирмы «АГ» (ФРГ) в 25-т тигельной индукционной печи промышленной частоты за 8-недельный период без смены футеровки было выплавлено 3100 т чугуна и стали. Большая часть выплавленного металла составляла коррозионностойкая хромоникелевая сталь [14].
Срок службы кислой футеровки в значительной мере зависит от качества исходного сырья. Для футеровки тигельных печей для плавки черных металлов и медных сплавов чаще всего используют кварциты двух месторождений — Первоуральского на Урале и Овручского на Украине. Первоуральский молотый кварцит марки ПКМИ-97,5 готовый к применению, выпускается Первоуральским динасовым заводом, а Овручский марки ПКМ-97 — Красногоровским огнеупорным заводом (табл. 2.). С точки зрения качества и технологии изготовления тиглей эти кварциты не равнозначны. При обжиге в кусках при 1600 °C пористость Первоуральского кварцита увеличивается до 14 %, а Овручского до 7,7 % [11] . Поскольку при выплавке стали температура металла может превышать 1600 °C, то применение более разрыхляющего в обжиге кварцита менее желательно, так как это приведет к большему насыщению футеровки металлом и шлаками, а следовательно, к увеличению скорости износа тигля. При плавке медных сплавов более высокая пористость кварцитов также приводит к уменьшению стойкости футеровки.
Таблица 2. Свойства кварцитов различных месторождений
Параметр | Месторождения кварцитов | |||
Овручское | Первоуральское (гора Караульная) | Антоновское | Тарасовское | |
Химический состав, % | ||||
SiO2 | 97,0-98,3 | 98,18-99,10 | 99,21 | 96,4-99,0 |
Al2O3 | 0,46-1,71 | 0,15-0,70 | 0,24 | — |
Fe2O3 | 0,1-0,57 | 0,14-0,42 | 0,11 | 0,12-0,59 |
CaO | 0,06-0,50 | 0,08-0,50 | 0,10 | 0,19-0,76 |
MgO | 0,90-0,10 | — | 0,5 | — |
TiO2 | 0,09-0,10 | 0,1 | — | — |
R2O3 | 0,18-0,30 | 0,15 | 0,13 | — |
Огнеупорность, °C | 1770 | 1770 | 1750-1770 | 1760 |
Плотность, г/см3 | 2,65-2,66 | 2,65-2,66 | 2,64 | 2,42-2,52 |
Пористость | 0-1,1 | 0,15-0,30 | 2-3 | 2,4-3,5 |
Массовая доля кремнезема в Первоуральском кварците выше (97,5-99 %), чем в овручском (97-98 %). Более высокая степень чистоты первоуральского кварцита обеспечивает однородность свойств материала и позволяет сократить существующие колебания в стойкости футеровки, что особенно важно при эксплуатации печей большей емкости. Первоуральский молотый кварцит марки ПКМИ-97,5 рекомендуется как оптимальный материал для кислой футеровки (см. табл. 2).
Для футеровки печей малой и средней емкости часто используют местные кварцевые пески с высоким содержанием кремнезема ( ≥ 97,5 %), для восполнения недостающих тонкомолотых фракций в футеровочную массу добавляют тонкомолотый кварцевый песок марки КП-1 или природный маршалит. Завод «Центролит» в г.Каунасе использует крупную фракцию высококачественных песков Аникшяйского рудника (Литовская ССР). Они содержат 97,68-98,67 % SiO2; 0,50-0,71 Al2O3 и 0,14-0,36 Fe2O3, огнеупорность 1730-1750 °C. Для восполнения недостающих мелких фракций в песок добавляют около 20 % естественного маршалита, поставляемого с Болотовского карьера (Челябинская обл.). Маршалит содержит 94-95 % SiO2; 2,7-2,8 % Al2O3 и 0,25 % Fe2O3.
Зерновой состав смеси, % | |
2,5-0,63 мм | 40-45 |
0,63-0,1 мм | 15-20 |
< 0,1 мм | 40-45 |
Длительный срок службы футеровки на этом заводе (3 мес) обеспечивается высоким качеством производства работ, чистотой кварцевого песка, получаемого в виде отсева крупных фракций на Паневежском стекольном заводе. В смеси с маршалитом в набивной массе содержание SiO2 равно не менее 97 %; Al2O3 не более 0,9 %; Fe203 не более 0,5 %; СаО не более 0,3 %; Na2O3 + К2О3не более 0,15 %.
На Горьковском и Волжском автозаводах вместо борной кислоты (1,5-2 %) применяют добавку борного ангидрида (0,6-0,8 %). Применение тонкоизмельченного борного ангидрида уменьшает количество влаги в футеровке, дает более тщательное смешивание с кварцитовой массой в мешалке и повышает равномерность спекания футеровки, что увеличивает ее стойкость.
Удельный расход футеровочной массы на тонну выплавляемого чугуна колеблется в широких пределах; от 2-3 кг/т на передовых предприятиях (ВАЗ, ГАЗ, Центролит) до 15-20 кг/т на заводах, пользующихся местными песками и кварцитами собственного помола. Такие колебания в расходе футеровочных материалов свидетельствуют о том, что для повышения производительности и надежности работы тигельных печей для чугуна необходимо пользоваться высококачественным молотым кварцитом централизованной поставки марки ПКМИ-97,5, который удовлетворяет требованиям по влажности (0,3 %), химическому, зерновому и минералогическому составу.
Основные данные для выбора вида футеровки индукционных тигельных печей приведены в табл. 1, 2.
Испытания опытной партии первоуральского кварцита влажностью 3 % на Мичуринском литейном заводе показали, что влажная футеровка не обеспечивает надежную работу печи потому, что влажный кварцит неравномерно уплотняется в стенке футеровки, при сушке влажной футеровки борная кислота, обеспечивающая спекание кварцита, мигрирует вместе с влагой в сторону индуктора. Перенос борной кислоты влагой приводит к плохому спеканию слоя футеровки, прилегающего к расплаву, и к спеканию буферного слоя, прилегающего к индуктору. Для нормальной работы футеровки необходимо, наоборот, хорошее спекание рабочего слоя и отсутствие спекания в буферном слое.
Применение влажного кварцита резко снизило стойкость футеровки печи ИЧТ-6. В результате простоя на ремонтах производительность печи снизилась на 40 %. Применение влажного кварцита увеличивает срок сушки и пуска печи в эксплуатацию и тем самым дополнительно снижает производительность печи. При получении влажного кварцита необходимо организовать его сушку на месте в электрических или газовых сушилках.
В ФРГ большинство индукционных тигельных печей футеруют кварцитом [15]. В Англии и США чаще применяют основные, высокоглиноземистые и шпинельные материалы. В Чехословакии, ГДР и других странах СЭВ предпочтение отдают кварцитным набивным массам [16-18]. Однако кислая футеровка не всегда позволяет соблюдать требуемые технологические параметры, даже при плавке высокосортного чугуна. При высоких температурах она быстро изнашивается; перегрев чугуна от 1450 до 1550 °C увеличивает износ стенки тигля в 3 раза [19]. Известно также, что кремний кислой футеровки активнее восстанавливается углеродом при повышении температуры, в результате чего увеличивается его содержание в металле. Кроме того, при выплавке чугуна с шаровидным графитом в печи необходимо проводить предварительную десульфурацию чугуна карбидом кальция, что уменьшает стойкость кислой футеровки тигля на 25-30 %. Стойкость нейтральной футеровки, состоящей из 40 % электроплавленого корунда и 60 % дистенсиллиманитового концентрата, не зависит от обработки чугуна карбидом кальция; такая футеровка показала лучшую стойкость по отношению к кислым и основным шлакам [20].
При выплавке синтетического чугуна общий угар и безвозвратные потери металла в случае использования нейтральной футеровки на 20-25 % меньше, чем при применении кислой футеровки, причем шлакообразование снижается на 30-35 %. Резко снижается угар Сr и Мg, выплавленный чугун содержит меньше газов и неметаллических включений [18].
Таким образом, с точки зрения металлургической технологии синтетического чугуна с шаровидным графитом, нейтральная футеровка предпочтительнее кислой. Нейтральная футеровка более устойчива к основным шлакам, чем кислая. При температуре металла выше 1400 °C износ нейтральной футеровки увеличивается и достигает максимальных значений при основности шлака 1,6-2,0 и содержании в нем FeO более 7 % [21]. Шлак индукционной плавки содержит от 4 до 10 % оксидов железа. Длительная эксплуатация печей с футеровкой на основе корунда и дистен-силлиманитового концентрата показала, что срок ее службы не превышает одного месяца.
Испытания муллитокорундовой и муллитовой футеровок [22] из набивных безусадочных масс на фосфатной связке (МК-90, ТУ 14-8- 457-84 и МЛМ-1, МЛ-2 по ТУ 14-8-119-74) показали высокую стойкость тигля. Для повышения плотности и содержания корунда в связке в массу добавляли 20 % электрокорунда (шлифпорошок 14А — ГОСТ 3647-80) и 3-4 % (сверху 100 %) ортофосфорной кислоты плотностью 1,57 г/см3. Стойкость футеровки превысила стойкость кварцитной футеровки, а также спекаемой футеровки на основе корунда и дистенсиллиманитового концентрата в 3-4 раза. В печи МГП-102 при плавке высоколегированной стали 25Л; при перегреве металла до 1710 °C футеровка прослужила более 2 мес. В печи ИЧТ-1 при плавке синтетического чугуна с шаровидным графитом стойкость футеровки составила 4 мес [22]. Наибольшее разъедание футеровки наблюдалось в шлаковом поясе при выплавке синтетического чугуна с содержанием в шихте до 80 % металлизованных железорудных окатышей (массовая доля Fe 79,2 %). При этом на поверхности металла образовалось более 15 % шлака (от массы плавки), содержащего до 20 % оксидов железа. Температура нагрева расплава составляла 1570 °C. Химический состав чугуна, %: 2,78 С; 0,1 Si; 0,009 Мg; 0,005 S; 0,01 Р. В печи было проведено более 100 плавок при 85 теплосменах до полного охлаждения тигля.
Основную футеровку изготавливают из магнезитовых, доломитовых и известковых огнеупоров, которые имеют химически основной характер. Эти материалы отличаются высокой огнеупорностью, как правило, выше 2000 °C. Химически чистые разновидности оксида магния имеют температуру плавления 2800, а оксид кальция 2500 °C.
В настоящее время для изготовления основной футеровки открытых тигельных печей применяют спеченный и плавленый магнезит, а для футеровки вакуумных печей — плавленый магнезит с содержанием MgO > 90 %. Для компенсации усадочных процессов при образовании шпинели в футеровочную массу добавляют от 10 до 30 % электрокорунда. С этой же целью вместо электрокорунда в массу добавляют 3-4 % молотого кварцевого песка, кварцита или молотого ферросилиция в количестве до 10 %. В качестве плавней, обеспечивающих спекание футеровки, обычно добавляют плавиковый шпат CaF2 [12], который при обжиге до 1400 °C способствует росту магнезитовой массы, а при 1500-1600 °C уменьшает усадку при спекании по сравнению с другими спекающими добавками (борной кислотой, бурой, стеклом, содой, криолитом).
Срок службы основной футеровки колеблется в зависимости от марок выплавляемой стали и от последовательности, с которой они выплавляются. Например, если вести подряд несколько плавок низкоуглеродистой стали, а затем несколько плавок высокомарганцевой, то футеровка пострадает значительно меньше, чем в том случае, если чередовать указанные металлы через плавку. Износ большинства составов периклазовой футеровки происходит в результате одновременного действия эрозии и коррозии, главным образом, на уровне зеркала металла. Сильно разрушается футеровка при неудовлетворительном качестве связки (мало тонких фракций, плохое спекание, дефекты набивки, разрыхление связки при спекании). Например, футеровка из магнезита и циркония имеет рост при обжиге и разрыхляется, ее шлакоустойчивость ниже, чем у магнезитовой с добавкой электрокорунда или кварцевого песка, что ограничивает ее применение.
Большое значение для стойкости футеровки имеет также чистота шихты, загружаемой для плавки. В условиях работы открытых индукционных печей завода «Электросталь» емкостью 1-1,3 т оптимальной является масса следующего состава: магнезитовый порошок 4-2 мм — 10 %; 2-1 мм — 14 %; менее 1 мм — 14 %; магнезитохромитовый порошок 4-2 мм — 10; 2-1 мм — 15 %; менее 1 мм — 35 %; плавиковый шпат менее 0,1 мм — 2 %.
Для размола компонентов массы используют, как правило, отработанный сводовый кирпич дуговых электропечей, очищенный от ошлакованных частей, пропитанных железистыми оксидами (ТУ 14-8-172-75). Применяют также магнезитовый порошок марок ПМЭ-88, ПМИ-88 по ТУ 14-8-209-76 с рассевом по фракциям 4-2 мм, 2-1 мм и мельче 1 мм или ППГ10И-90 по ТУ 14-8-149-75.
Для приготовления набивной массы составные части тщательно смешивают в лопастном смесителе или в бегунах. Срок хранения готовой массы в условиях, не допускающих увлажнения и загрязнения пылью, не ограничивается. Стойкость футеровки на печи ИСТ-1,0 составляет 40-50 плавок. В индукционных печах (для плавки стали) меньшей емкости ( ≤ 0,5 т) футеровка аналогичного состава имеет стойкость 70-90 плавок.
На малых печах (ИСТ-0,06 т) набивку тиглей производят увлажненной массой, состоящей из 49 % периклазового и 51 % периклазохромитового порошков со следующим зерновым составом смеси: 4-2 мм — 20 %; 2-1 мм — 30 %; мельче 1 мм — 50 %. Увлажненную массу перед укладкой рекомендуют выдержать под мокрой мешковиной не менее 16 ч, но не более 36 ч. Степень увлажнения массы такова, что при сжимании ее в руке комок не рассыпается, но легко разваливается при давлении пальцем.
Основная футеровка разных составов и даже из плавленого магнезита с электрокорундом имеет сравнительно низкую стойкость и не всегда обеспечивает надежную работу индукционных тигельных печей. Основная причина этого состоит в том, что все разновидности магнезитовых набивных масс, наряду с положительными свойствами (высокая огнеупорность, шлако- и металлоустойчивость), имеют ряд существенных недостатков. Главной причиной низкой стойкости основной футеровки (особенно в печах повышенной емкости > 500 кг) является неудовлетворительное ее объёмопостоянство и термостойкость. В процессе службы длительное воздействие на футеровку высоких температур, их резкие колебания, а также диффузия расплавов металла и шлака в толщину стенки тигля через постепенно развивающиеся трещины в спекшейся части футеровки приводят к более глубокому спеканию тигля, большим усадкам и к образованию глубоких трещин. Причем величина трещин тем больше, чем больше объем огнеупорного тигля. Для увеличения стойкости периклазовой футеровки в нее вводят хромит или применяют смесь периклазовых и периклазохромитовых компонентов (см. табл. 1, п.8).
Данные о продолжительности службы основной набивной футеровки в производственных условиях крайне разноречивы и имеют большие колебания (от 10-15 до 70-80 плавок). Слабым звеном в тигле является шлаковый пояс, где футеровка обильно насыщается из шлака оксидами SiO2; CaO; MgO; R2O. Массовая доля MgO в рабочей зоне шлакового пояса снижается до 21 %, Fе2O3увеличивается до 8 %, а содержание силикатов возрастает примерно в 4 раза, огнеупорная форстеритовая связка перерождается в неогнеупорную монтичеллиуовую. При температуре расплава 1600-1640 °C при постоянном снабжении футеровки шлаками наблюдается разрушение агрегатных скоплений, а также отдельных зерен периклаза и зерен образовавшейся шпинели при обжиге футеровки. В результате чего образуется менее устойчивая структура с корродированными зернами периклаза и шпинели, разобщенными силикатными прослойками, и с отдельными участками, состоящими из менее огнеупорных силикатов. Такая структура менее износоустойчива в службе и обусловливает высокий износ шлакового пояса тигля вследствие оплавления.
Износ футеровки стен основного тигля ниже уровня шлака значительно меньше. Поступление силикатных расплавов в эти участки футеровки ограничено, вследствие чего резко различаются состав и структура после службы рабочей зоны нижней части стен тигля от структуры шлакового пояса.
Использованная литература:
1. Сасса В.С. Футеровка индукционных печей. М.: «Металлургия», 1989, 232 с.
Данная статьи была взята из этого первоисточника.