Шахтные печи для цементации и других видов химико-термической обработки (ХТО) сталей часто используются в серийном производстве стальных изделий. Для массового производства чаще применяют безмуфельные печи методического действия.
Цементация в шахтных печах сопротивления с газообразным или жидким карбюризатором (веществом-донором атомов углерода) происходит в 1,5 раза быстрее, чем при использовании твердого карбюризатора.
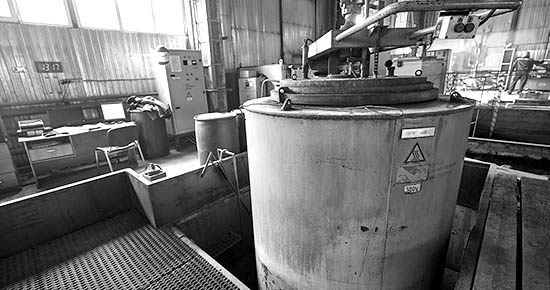
Шахтные цементационные печи относятся к установкам периодического действия, поэтому не подходят для массового производства, но оптимальны для серийного. Они комплектуются ретортами для загрузки партий деталей и прочим оборудованием для подачи газовой смеси или жидкости в рабочий объем.
СШЦМ относятся к печам с вертикальной загрузкой и могут использоваться для ХТО и последующей термической обработки деталей.
Конструктивные особенности печей СШЦМ
Конструкция конкретной цемементационной печи напрямую зависит от поставленных перед ней задач, доступного пространства в производственном помещении. Но любая подобная установка имеет основные конструктивные элементы:
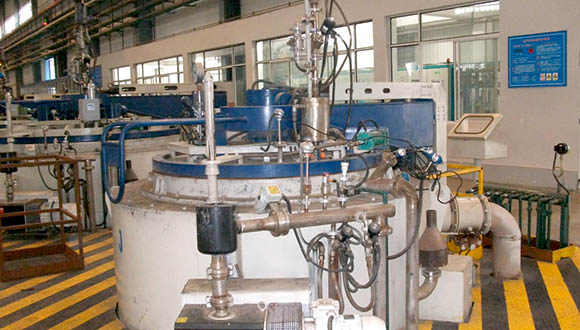
- Корпус из листового металла.
- Футеровка из огнеупоров с нагревательными элементами в виде лент или проволоки из фехрали, нихрома или других сплавов сопротивления, подходящих для применения в среднетемпературных печах.
- Реторта из жаропрочного сплава или чугуна (в зависимости от температурного режима установки), установленная в корпус. В реторту загружается подготовленная садка.
- Крышка с разъемами для подачи газа печной атмосферы, затвором сброса и другими конструктивными элементами.
- Механизм подъема и поворота крышки с электромеханическим приводом.
- Пульт управления с тиристорными преобразователями электроэнергии, подаваемой на нагревательные элементы.
- Система подготовки печной атмосферы (газовая стойка) с ручным или автоматическим управлением.
Тип и конфигурация каждой детали и узла определяется на стадии проектирования с учетом выполненных предварительных расчетов требуемой производительности и режимов работы.
Цементационные печи сопротивления устанавливаются в технологические углубления в производственных помещениях или непосредственно на пол.
Основные параметры каждой печи указываются в ее маркировке. В частности, в числовой составляющей указаны высота с диаметром рабочей области и номинальная температура. Несмотря на особенности конструкции, принцип работы всех шахтных цементационных печей схож.
Принцип работы печей СШЦМ
Детали перед загрузкой в печь подготавливаются соответствующим образом: поверхность очищается от загрязнений, а участки, которые не требуют цементации, защищаются специальной обмазкой. Затем подготовленные детали собираются в садку.
Готовая садка загружается в разогретую до рабочей температуры печь. Время выхода на рабочую температуру и время ее выдержки задается на пульте управления. В рабочий объем подается газообразный карбюризатор (метан, пропан и другие газы в смеси, эндогаз).
Если крышка печи оснащена капельным устройством, то могут применяться жидкие карбюризаторы, которые также дозировано подаются в рабочее пространство, где жидкость переходит в состояние газа. 1 кубический сантиметр жидкого карбюризатора в среднем содержит 23 капли.
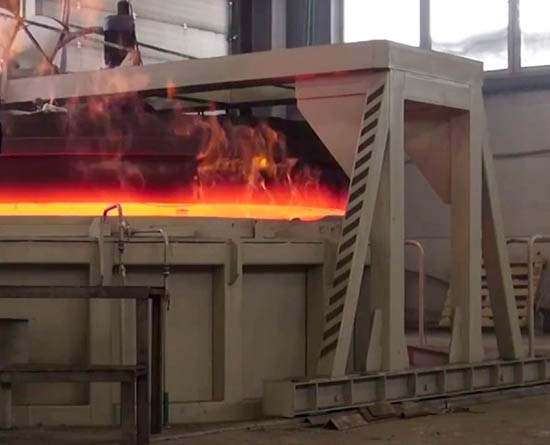
Садка выдерживается при заданной температуре и атмосфере в течение времени, необходимого для формирования цементированного слоя требуемой толщины.
Расход карбюризатора в цементационных печах
Параметр печи | Расход жидких карбюризаторов (керосина, пиробензола, синтина) в каплях в минуту | Расход природного газа в м3/ч | |||
Объем рабочего пространства, м3 | Производительность в кг/ч при глубине цементации в 1 мм | При нагреве | При выдержке | При нагреве | При выдержке |
0,04 | 100 | 25—35 | 60—70 | — | — |
0,08 | 150 | 35—45 | 60—90 | 0,3—0,5 | 0,9—1,2 |
0,14 | 220 | 35—45 | 70—90 | 0,3—0,5 | 0,9—1,2 |
0,25 | 400 | 50—75 | 120—150 | 0,4—0,6 | 1,2—1,6 |
0,35 | 600 | 50—75 | 120—150 | 0,4—0,6 | 1,2—1,6 |
0,85 | 1500 | 60—80 | 150—170 | 0,4—0,6 | 1,2—1,8 |
0,03 | 50 | 25—35 | 40—60 | — | — |
0,10 | 150 | 35—45 | 60—90 | 0,3—0,5 | 0,9—1,2 |
0,14 | 220 | 35—45 | 70—90 | 0,3—0,5 | 0,9—1,2 |
0,34 | 660 | 50—75 | 120—150 | 0,4—0,6 | 1,2—1,6 |
Излишки газа сбрасываются через затвор сброса и сгорают в атмосфере рабочего помещения.
После цементации в шахтной печи сопротивления детали могут проходить последующую термическую обработку в требуемом режиме. Распространено применение следующих режимов обработки деталей после цементации:
- Подстуживание — закалка — низкий отпуск (сниженное коробление).
- Охлаждение — закалка — низкий отпуск (отсутствует образование карбидной сетки).
- Охлаждение — высокий отпуск — закалка — низкий отпуск (увеличенная твердость низколегированных сталей).
- Подстуживание — закалка — обработка отрицательной температурой — низкий отпуск (резкое повышение поверхностной твердости при остаточном растворе углерода в поверхностном слое).
- Охлаждение — закалка — обработка отрицательной температурой — низкий отпуск (резкое повышение поверхностной твердости при остаточном растворе углерода в поверхностном слое).
- Охлаждение — нормализация — закалка — низкий отпуск.
После обработки детали проходят все требуемые этапы контроля качества, и готовы к эксплуатации.
Достоинства шахтных цементационных печей
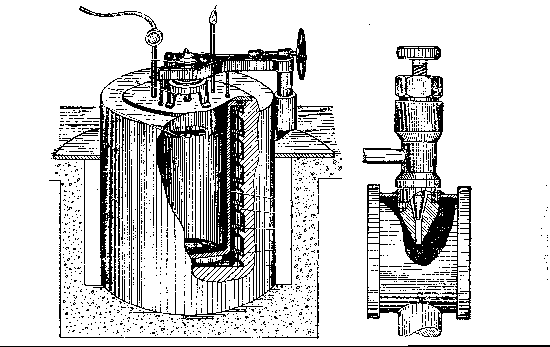
Цементация в газообразном карбюризатор происходит быстрее, чем в твердом, но медленнее, чем в соляных ваннах. Цементация в тлеющем разряде сопоставима с газовой, но распространена гораздо менее.
Цементация сталей в твердом карбюризаторе технологически проще, поэтому до сих пор широко применяется в кустарном производстве. Для серийного и массового производства технология не подходит.
Сложно процесса газовой цементации и более высокие требования к квалификации персонала уравновешиваются достоинствами технологии:
- Более низкая стоимость, чем у цементации в расплавах солей.
- При более высокой квалификации, количество персонала, необходимого для работы печи, ниже.
- Возможность последующей температурной обработки изделий.
- Более точное регулирование процесса и концентрации углерода в печной атмосфере.
- Высокая степень автоматизации процесса в целом.
Таким образом, шахтные печи сопротивления для цементации — установки, которые обеспечивают химико-термическую обработку стальных деталей с оптимальной для серийного производства эффективностью.