Вакуумная индукционная плавка (ВИП) — процесс плавки металлов в индукционных печах в вакууме. Промышленное значение технология приобрела в 1950-х., когда практика показала увеличение срока службы и качества жаростойких и суперсплавов с высоким содержанием алюминия и титана, полученных плавкой в вакууме.
Технология подтолкнула развитие реактивных двигателей в военной и гражданской авиации. Турбины с деталями из сплавов, полученных при помощи ВИП, отличались повышенной производительностью и надежностью.
Успешное производство качественных суперсплавов для турбинных двигателей с применением вакуумной индукционной плавки пробудил интерес к использованию материалов в других областях, например, для ядерных ректоров и электроники. Вдобавок, низкие потери материалов сделали процесс экономически выгодным для получения некоторых ценных сплавов с невысокими требованиями к чистоте.
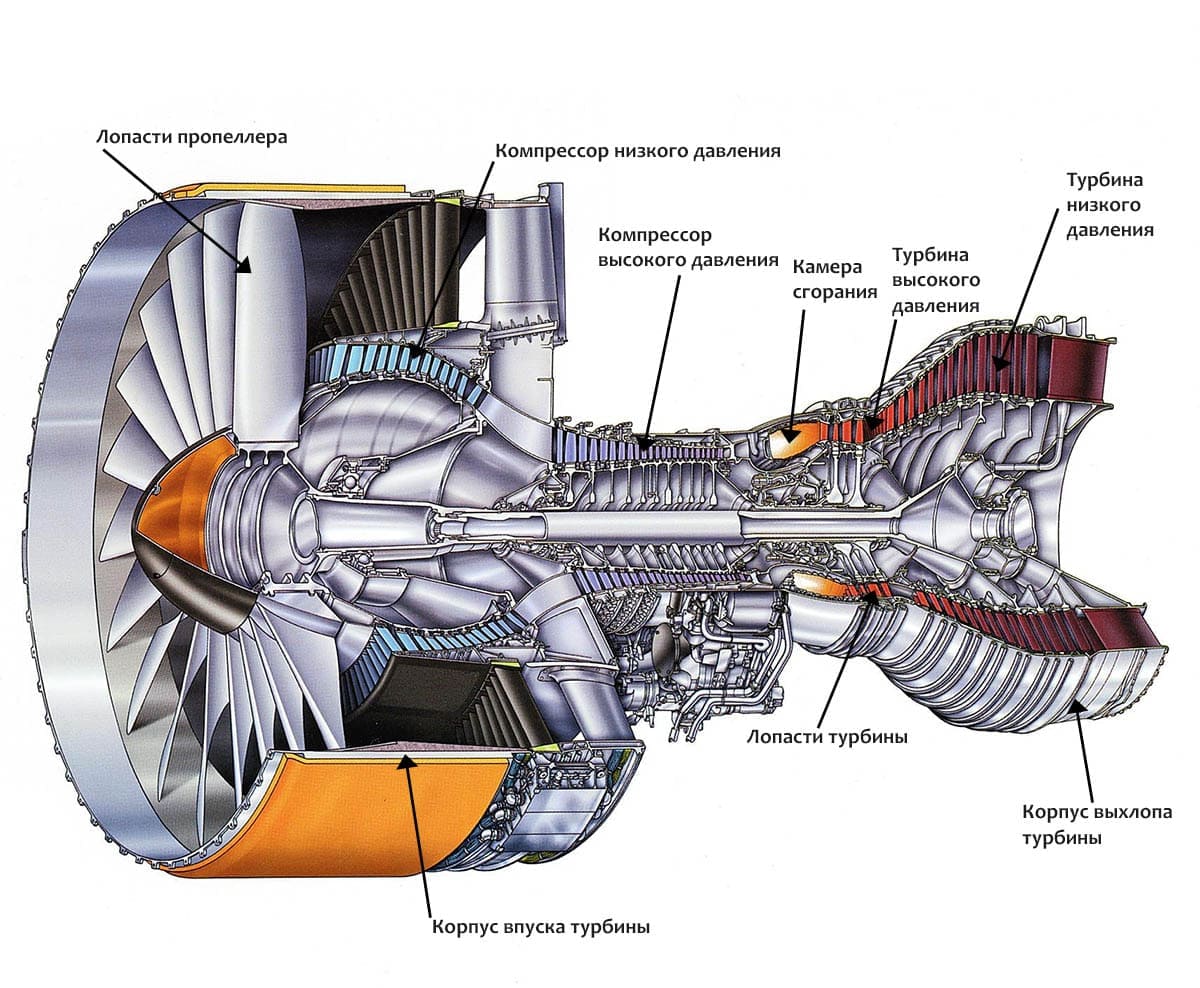
Рис. 1: Титановые лопасти пропеллера и лопасти турбины из суперсплавов, полученных путем индукционной плавки в вакууме, критически важны для современных производительных реактивных двигателей. Они используются в двигателях Pratt and Whitney PW4000, которые, в частности, устанавливаются на Boeing 747.
Достоинства вакуумной индукционной плавки:
- Удаление газов. При очень низком давлении (0,000001 атм.) загрязняющие газообразные вещества и другие нежелательные элементы покидают исходный материал в процессе плавки.
- Точный контроль химического состава. При отсутствии атмосферы количество элементов и соединений в реакциях проще контролировать.
- Превосходный контроль процесса. Независимый контроль давления, температуры и индукционного перемешивания позволяет создавать различные технологические процессы для получения сплавов с требуемыми свойствами.
- Бесшлаковое плавление. Плавление в вакууме исключает необходимость в защитном слое шлака на зеркале расплава. Заодно исключается и вероятность загрязнения готового материала шлаком.
- Защита расплава. Высокий вакуум предупреждает загрязнение расплава реакциями с газами, содержащимися в атмосфере.
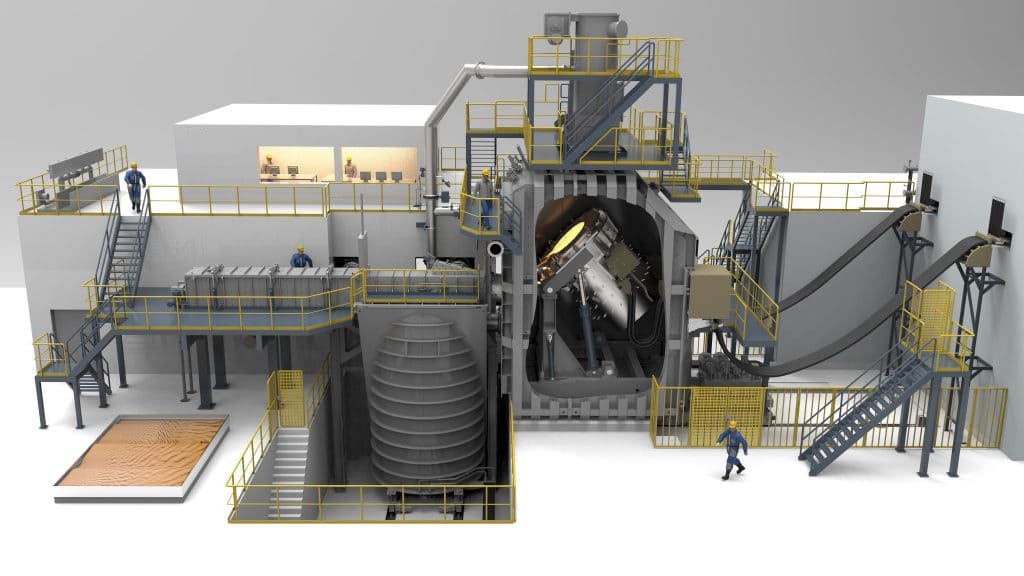
Описание процесса
Процесс ВИП сам по себе предельно прост, но необходимое для него оборудование достаточно сложно. Для обеспечения оптимальной продуктивности все компоненты требуют аккуратного обслуживания, тестирования и калибровки. Схематический план типичного комплекса промышленного оборудования приведен на рисунке 2.
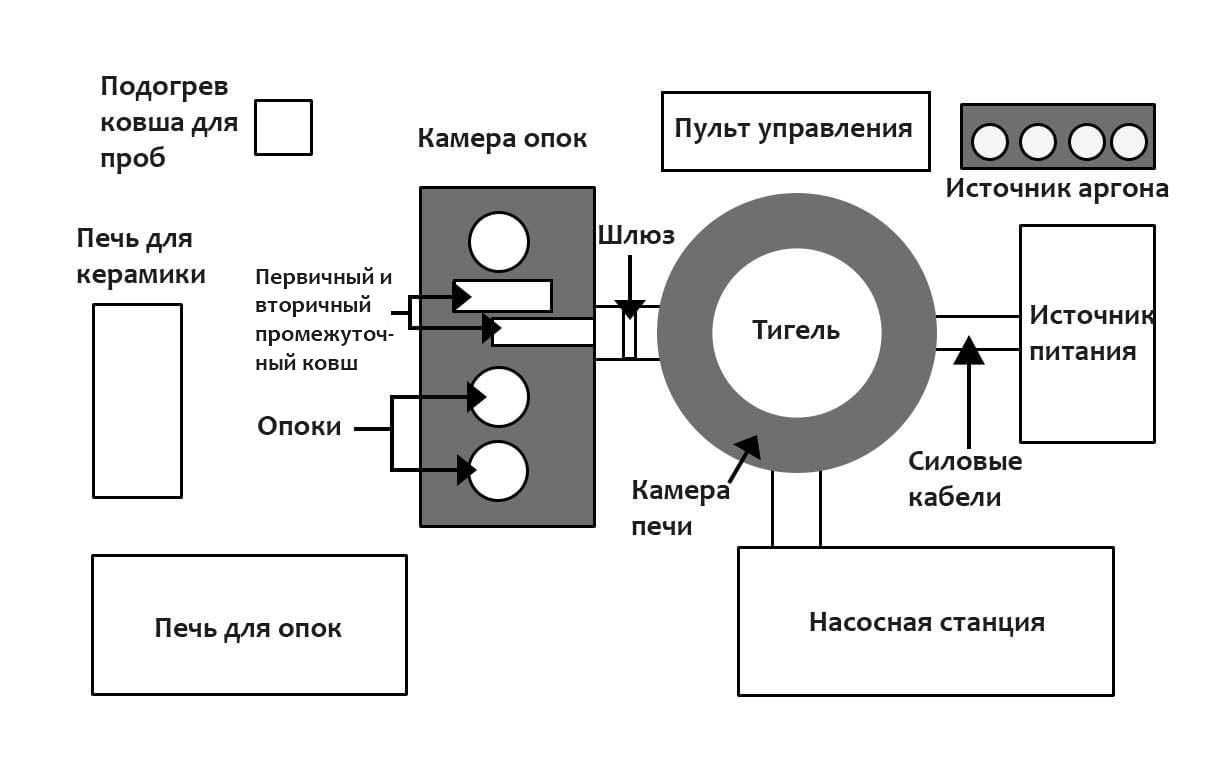
Рис. 2: Комплекс оборудования для вакуумной индукционной плавки требую систем электропитания, вакуумных насосов, подачи инертного газа и, обычно, предварительного подогрева опок.
Как видно, комплекс состоит из:
- камеры плавления;
- камеры подготовки опок;
- насосная система;
- источника питания;
- пульта управления.
Камера плавления включает в себя жаропрочный тигель, окруженный индуктором. Последний одновременно обеспечивает плавление металла и перемешивание расплава. Оборудование для завалки, контейнеры с присадками, инструменты для взятия проб и контроля, как правило, хранятся над камерой для упрощения доступа к поверхности расплава. Все подобные камеры изолированы от основной и вентилируются отдельно для предотвращения загрязнения сплава.
В камере подготовки опок хранятся опоки для свитков, установлены первичный и вторичный промежуточный ковш, а также расположены прочие инструменты. Камера продувается отдельно, чтобы печь могла работать в полунепрерывном режиме.
Конструкция вакуумной индукционной печи позволяет начинать следующий производственный цикл до начала предыдущего. Благодаря изолированной камере для опок очередная плавка может быть начата, пока остывают слитки предыдущей партии.
Система подачи аргона также подключена к камере подготовки опок для заполнения инертным газом в случае возникновения чрезвычайных ситуаций.
Конструкция насосной системы конкретной печи зависит от:
- объема тигля;
- типов сплавов;
- требуемой скорости откачивания воздуха;
- предельного вакуума, требуемого для типичной системы.
Механический форвакуумные насосы, воздуходувки и паровые насосы объединяются в системы с оптимальной скоростью нагнетания вакуума при минимальных операционных расходах. Давление в плавильной камере типичной печи для ВИП показано в диаграмме на рисунке 3.
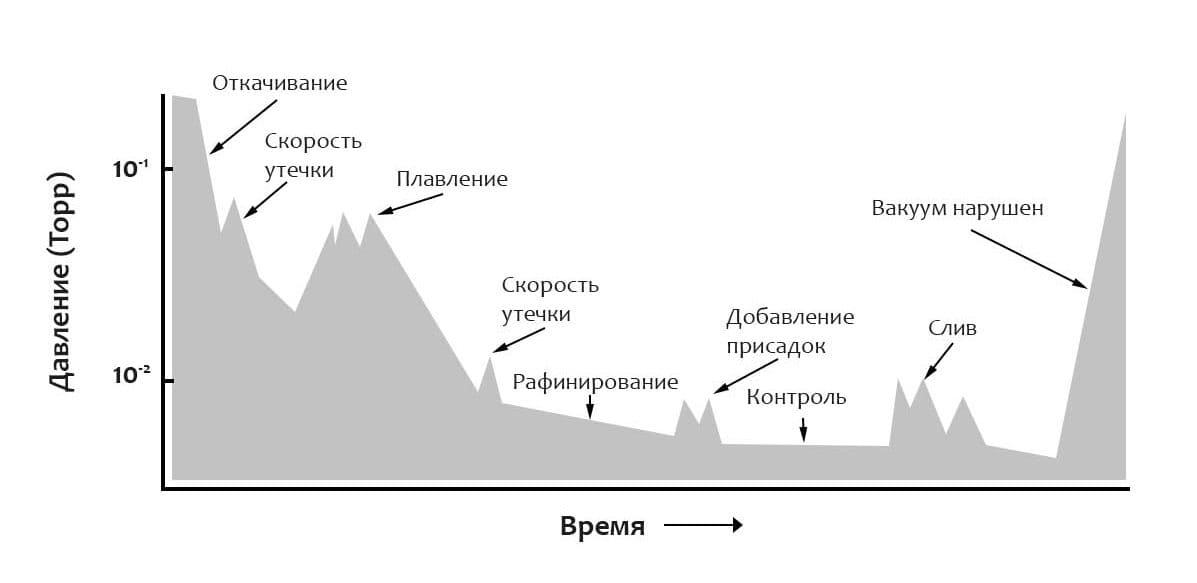
Рис. 3: Давление в рабочем объеме печи меняется с переходом от одной стадии обработки к другой.
Источник питания для большинства больших печей — это мотор-генераторный узел, способный производить примерно 4,2 мВт при 180 гЦ.
Пульт управления из всех переключателей, кранов, чувствительного и записывающего оборудования, которое служит для управления процессом плавки. Наблюдение за процессом плавки осуществляется непосредственно через защищенные смотровые окна или при помощи видеокамер соответствующего типа.
Кроме собственно печи значительное количество электроэнергии потребляют также печи для предварительного нагрева опок, промежуточных ковшей, прочей керамики и инструментов для забора проб. Нагрев в таких печах может осуществляться посредством масла, газа или электричества.
Электричество позволяет нагревать инструменты и принадлежности без отложений химических элементов. Например, мельчайшие следы серы или углерода на ковшах для забора проб способны исказить показания химического анализа.
Конкретные процедуры и технологии изготовления тех или иных сплавов не разглашаются производителями, однако, в любом процессе индукционной плавки в вакууме есть несколько основных этапов.
Первый этап
После завалки сырья включается насосная станция, создающая вакуум. Для контроля стабильности системы в процессе периодически проверяется скорость утечки. По достижении требуемого давления на индуктор подается ток плавления.
Второй этап
В процессе плавления давление, как правило, неустойчиво. Оно колеблется во время расплавления различных компонентов сырья. Если кипение становится слишком интенсивным, то в камеру плавления подается аргон.
После полного расплавления партии сырья наведение вакуума продолжается до достижения 10—2-10—3 Торр и постоянной скорости утечки. Стабильная скорость утечки предполагает близость завершения раскисления.
Третий этап
На этой стадии производства сплавов в них вводятся присадки. В процессе плавления реактивов выделяется газ, и наблюдается небольшое повышение давления.
Четвертый этап
Забор проб для проведения анализов и подтверждения соответствию технологическим условиям и требованиям к конкретному сплаву.
Пятый этап
После получения положительных результатов анализа открывается летка для слива расплавленного металла в промежуточный ковш, расположенный в камере подготовки опок.
Первичный промежуточный ковш оснащен перегородками для контроля скорости потока металла и улавливания фрагментов футеровки или тигля.
Из первичного промежуточного ковша металл истекает во вторичный. Во вторичном ковше размещены дополнительные перегородки вместе каналами, которые направляют расплавленный металл в опоки. Выход газов сливной системы приводит к небольшому повышению давления.
Шестой этап
На этой стадии промежуточные ковши опустошаются и меняют положение в камере опок. Газовый шлюз закрывается; следующий цикл плавки может начинаться. После кристаллизации металла в опоках, вакуум в камере опок устраняется, и камера открывается. После этого начинается подготовка камеры к следующему циклу.
Таким образом, технология вакуумной индукционной плавки отличается, прежде всего, минимальным количеством загрязняющих газов в рабочем пространстве печи. Соответственно отличается и комплекс требуемого оборудования. Герметичные камеры, насосные станции и системы подачи инертного газа усложняют и удорожают оборудование, но обеспечивают высокое качество готовой продукции.