Концепция закалки металлов с нагревом токами высокой частоты появилась незадолго до начала ХХ века, а широкое применение в промышленности получила к его середине. Это экономный и эффективный метод повышения прочности деталей и заготовок из сталей с различным содержанием углерода. Подходит для массового производства, но оправдан и при единичном изготовлении деталей механизмов, которые подвергаются нагрузкам.
Для подобной обработки необходимо оборудование соответствующего типа. Конфигурация, диапазон рабочих частот и прочие параметры каждой установки рассчитываются с учетом материала, размеров и формы обрабатываемых деталей так же, как и требуемой глубины слоя закалки. Установки, предназначенные для обработки различных деталей, сложнее.
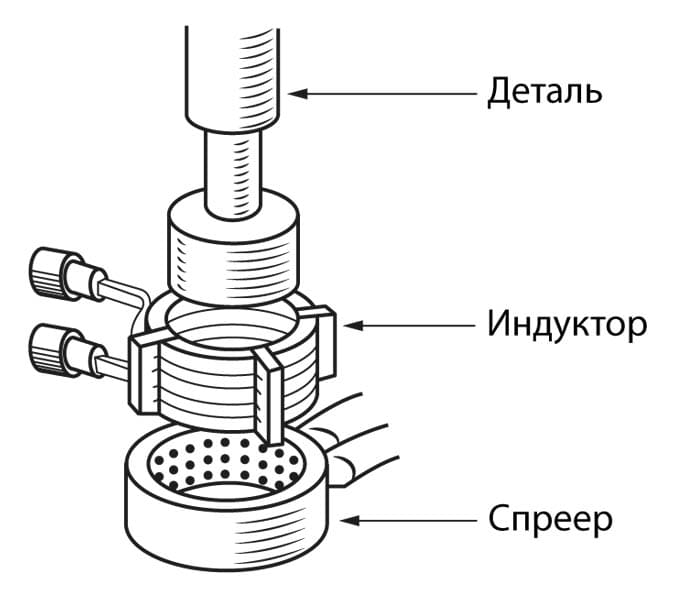
Индукционные закалочные установки (ИЗУ) применяются для термообработки широкого спектра изделий, начиная швейными иглами, и заканчивая крупногабаритными шестернями, валами и корпусами подшипников.
Основные системы индукционных закалочных установок
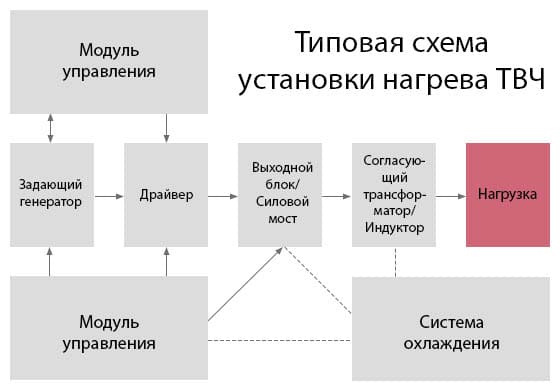
Независимо от конфигурации и типа обработки, каждая установка для ТВЧ закалки оснащается рядом основных систем:
- источник питания, в небольших установках совмещается в одном корпусе с преобразователем частоты;
- индуктор, часто совмещаемый со спреером, подающим на заготовку закалочный состав (воду, масло и прочие);
- охлаждение индуктора, тиристоров, трансформатора и других нагревающихся элементов.
- блок управления и прочие вспомогательные системы (механизмы вращения, перемещения деталей или индуктора, датчики температуры, автоматика и прочие).
Крупные установки чаще проектируются с источником питания, преобразователем, блоком управления и системой теплообмена в собственных корпусах. Система охлаждения таких установок с непрерывным рабочим циклом часто строится на базе градирен.
В случае с небольшими установками, используемым для объемного закаливания мелких деталей, все системы могут размещаться в едином корпусе (одноблочные установки). Источник питания и преобразователь частоты могут быть помещены в один шкаф, вместе с управляющим оборудованием (двублочные установки).
Проектируя установку для индукционной закалки токами высокой частоты, инженеры выбирают одно из наиболее подходящих типовых решений или приспосабливают его к требованиям технического задания.
В любом случае каждая установка проектируется на основе ключевых систем, параметры которых соответствуют условиям ее работы.
Источник питания/преобразователь частоты
Частота или диапазон частот тока, подаваемого на индуктор — основной параметр источника питания индукционной закалочной установки. Это один из основных параметров, определяющих глубину проникновения тока и, следовательно, толщину закаливаемого слоя.
Оптимальные схемы источников питания выбираются в зависимости от требований к процессу обработки и другим параметрам. Существует несколько типов ключевых элементов, которые используются в зависимости от условий работы будущей установки.
Тип ключевых элементов/Параметр | КПД | Оптимальные параметры тока | Срок службы | Достоинства | Недостатки |
Вакуумные лампы | 55-60% | Частота>300 кГц | 2000-4000 часов | Работа с токами высокого напряжения и силы, хорошая вольт—амперная характеристика. | Высокая стоимость, повышенная опасность при работе с высоким напряжением, малый ресурс. |
Транзисторы | 85-93% | Частота 10-50 кГц — IGBT Частота>50 кГц — MOSFET | Более 10 лет при соблюдении правил эксплуатации и обслуживания | Не требуется время для восстановления запирающих свойств, минимальные коммутационные потери, компактный размер, не нужен прогрев, малая мощность холостого хода, способны работать непрерывно. | Потребность в активном охлаждении, чувствительность к качеству входного напряжения. |
Тиристоры | 90-95% | Частота до 10 кГц |
Кроме того, источник питания для установок индукционной закалки токами высокой частоты состоит из нескольких блоков, которые в небольших установках объединены в одном корпусе, а в масштабных — могут быть собраны в собственных корпусах:
- конвертер или выпрямитель, преобразующий переменный ток промышленной частоты в постоянный (может оснащаться элементами для регулирования мощности или напряжения);
- инвертор, преобразующий постоянный ток в переменный с одной фазой и требуемыми параметрами;
- блок согласования, который, на основе данных автоматики или пульта управления, приводит ток, подаваемый на индуктор, к требуемым параметрам.
Большинство источников питания современных индукционных закалочных установок собираются по мостовой или полумостовой схеме. Оптимальная конфигурация выбирается в соответствии с требуемыми рабочими параметрами установки.
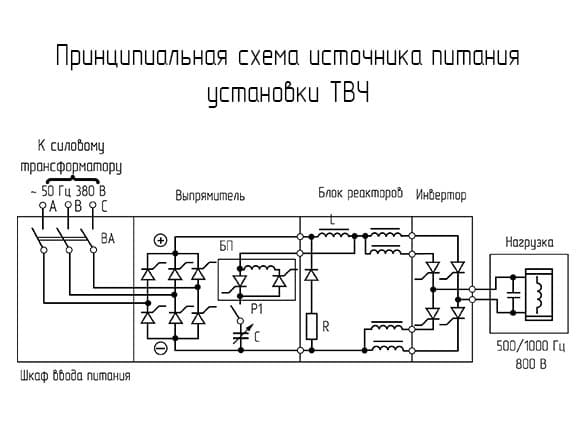
Проектируемый источники питания снабжаются системами защиты от перегрузок, охлаждением и прочими элементами, необходимыми для безопасной и стабильной работы установки.
Индуктор
Индуктор — основной функциональный элемент установки. Чаще всего изготавливается из круглой или профильной медной трубы. Это оптимальная конфигурация для подачи охлаждающей жидкости. В процессе закалки индуктор нагревается за счет сопротивления и тепла, излучаемого деталью.
Параметры магнитного поля, наводимого индукторами из труб круглого и квадратного сечения, практически не отличаются на небольших и средних установках.
Одна установка для закалки ТВЧ может комплектоваться несколькими типами индукторов для обработки валов, зубчатых колес и других изделий. Необходимый индуктор можно изготовить самостоятельно, но для этого понадобится правильно рассчитать количество его витков.
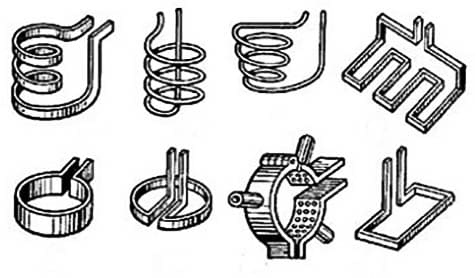
Выбор материала, меди, обусловлен его высокой проводимостью. В ряде специальных случаев могут применяться индукторы из серебра или его сплавов.
Конфигурация индуктора зависит от типа обработки:
- наружных поверхностей цилиндрических изделий;
- внутренних поверхностей цилиндрических изделий;
- наружных и внутренних поверхностей деталей сложной формы (конических, с переменным сечением и прочих);
- плоских поверхностей.
Различные конструкции индукторов обусловлены требованиями к процессу обработки. Для равномерного нагрева расстояние между индуктором и нагреваемым объектом должно быть одинаковым во всех точках Нагрев деталей различной формы в одном и том же индукторе недопустим.
КПД индукторов сравнительно низок. До 40% подаваемой на них энергии рассеивается в пространстве или расходуется на нежелательные магнитные явления. Для повышения коэффициента полезного действия индукторы установок закалки ТВЧ защищают магнитопроводами, которые концентрируют рассеиваемую энергию.
Индукторы требуемой конфигурации для закалки определенных деталей могут поставляться вместе с установкой сразу или быть изготовлены отдельно, в любой момент после ее ввода в эксплуатацию.
Управление
Модули управления современными закалочными установками ТВЧ строятся на основе микроконтроллеров или логических элементов. Диапазон функций, расположение органов управления и другие аспекты выполняются в соответствии с типовым проектом или техническим заданием заказчика.
В модуль управления поступают сигналы со всех датчиков. В нем же располагаются элементы управления всеми системами:
- питанием;
- охлаждением;
- подвижными элементами (индуктор, центры и прочие).
Таким образом модуль управления не только задает параметры работы всех исполнительных элементов, включая задающий генератор, но и анализирует их состояние.
Современные модули управления могут оснащаться блоками для соединения с интернетом для дистанционной диагностики, записи и хранения отчетов и других требуемых функций.
Охлаждение и вспомогательные системы
Исправно работающая система охлаждения соответствующей производительности необходима для нормальной работы любой установки. Ее конфигурация определяется нагрузкой на агрегат, бюджетом, параметрами производственного помещения и множеством других аспектов. Конфигурации варьируются между емкостью с насосом и градирней с теплообменным шкафом.
Кроме основных систем установки для закалки токами высокой частоты оснащаются дополнительными: управлением приводами центров, системами самодиагностики и защиты, а также многими другими.
Специалисты ТермолитПЛЮС разработают установку для индукционной закалки токами высокой частоты, которая будет полностью соответствовать режимам работы и прочим поставленным условиям.