Закалка алюминиевых деталей в жидком азоте – это цель, в которой изучают влияния криогенных закалочных сред на коробление и механические свойства деталей из алюминиевых сплавов.
Образцы из сплава Д16АМ после нагрева до 500 °С и выдержки в зависимости от толщины закаливали в жидком азоте. Нагревали образцы в воздушно-закалочных агрегатах. Для уменьшения испарения жидкий азот заливали в бак с двойными стенками. Для сравнения образцы после нагрева охлаждали в воде при 20 °С, в кипящей воде и на воздухе. После закалки и естественного старения определяли величину коробления и исследовали механические и коррозионные свойства образцов. Листовые образцы из сплава Д16АМ имели размеры 500×140×1,2 и 300×30×(1÷5) мм.
Исследования закалки в жидком азоте
Исследования показали, что средняя величина стрелы прогиба образцов, закаленных в жидком азоте, составляет примерно 1,5 мм, в то время как аналогичные образцы, закаленные в воде, имели стрелу прогиба в среднем 50 мм.
Таким образом, коробление образцов, закаленных в жидком азоте, уменьшается более чем в 30 раз. Такое значительное уменьшение коробления при закалке алюминиевых деталей в жидком азоте по сравнению с закалкой в воде объясняется различными механизмами охлаждения детали [1, 2].
Скорость охлаждения любого материала зависит от теплоемкости охлаждающей жидкой среды. При охлаждении в воде она неравномерно испаряется при соприкосновении с деталью; в результате скорость
передачи тепла между участками детали, находящимися в непосредственном контакте с водой, и соседними участками — в контакте с водяным паром — неодинакова. Различная скорость охлаждения вызывает неодинаковые степени сжатия материала при закалке и закалочные напряжения и, как следствие, деформацию материала.
Закалка в жидком азоте – образование газообразной пленки
Жидкий азот имеет более низкую теплоту парообразования по сравнению с водой. Так, если для воды удельная теплота испарения составляет 539 кал/г, то для азота она равна 47 кал/г, т. е. примерно в 10-11 раз меньше.
Следовательно, стадия образования газообразной рубашки гари закалке в жидком азоте не прерывается, вследствие чего достигается равномерное охлаждение поверхности и сечения детали на протяжении всего цикла охлаждения, что и предопределяет получение деталей с минимальной деформацией.
Таблица исследований закалки в воде и жидком азоте
Материал | Толщина металла в мм | σВ в кГ/мм2 | δ в % | σВ в кГ/мм2 | δ в % | σВ в кГ/мм2 | δ в % |
по ГОСТу и АМТу | После закалки в воде | После закалки в жидком азоте | |||||
Д16АМ, лист | 0,47 | 42 | 13 | 45 | 21 | 45 | 21 |
0,75 | 46 | 19 | 46 | 20 | |||
1,15 | 45 | 20 | 45 | 22 | |||
1,50 | 45 | 20 | 45 | 21 | |||
1,90 | 47 | 19 | 46 | 21 | |||
2,50 | 45 | 19 | 45 | 20 | |||
2,9 | 44 | 11 | 44 | 18 | 45 | 18 | |
3,8 | 45 | 19 | 45 | 18 | |||
4,8 | 46 | 14 | 44 | 17 | |||
Д16АМ, профиль | 2,11 | 40 | — | — | 45 | 21 | |
3,13 | 47 | 17 | |||||
4,12 | 46 | 20 |
Исследования показали (см. таблицу), что предел прочности и относительное удлинение незначительно отличаются от прочностных характеристик образцов, закаленных в воде, и находятся в пределах требований ГОСТа. Это соотношение справедливо для образцов с толщиной стенки до 5 мм. При толщине же стенки больше 5 мм прочностные характеристики образцов, закаленных в жидком азоте, начинают
уменьшаться, что связано с меньшей скоростью охлаждения в жидком азоте по сравнению со скоростью охлаждения в воде.
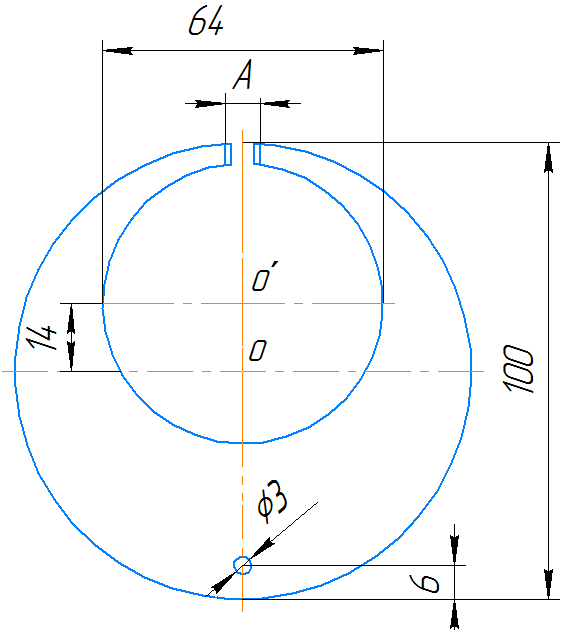
Рис.1. Кольцо Френча после разреза.
Остаточную деформацию алюминиевых сплавов, закаленных с различными скоростями, определяли на кольцах Френча (рис. 1), вырезанных из плакированного листа толщиной 5 мм сплава Д16АМ одной плавки. Величину деформации определяли по изменению расстояния А между рисками после резки на фрезерном станке с шириной прорези 2 мм. Первоначальное значение расстояния между рисками А было 10 мм. Образцы после нагрева при 500 °С и необходимой выдержки охлаждали в воде
при 20 °С, в кипящей воде, в жидком азоте и на воздухе.
По 10 колец Френча охлаждали в каждой среде. Средние значения деформаций после охлаждения в различных средах показаны на рис. 2.
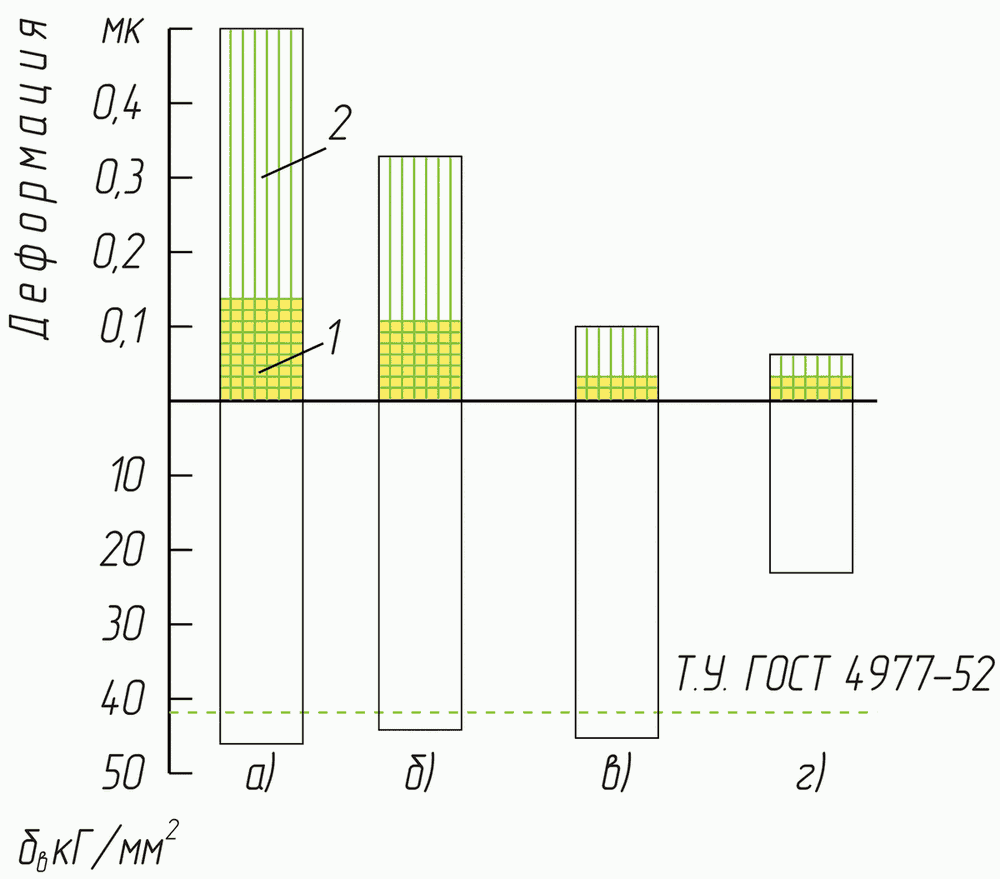
Рис.2. Деформация колец Френча после закалки в различных средах: а — в воде при 20 °С; б — в воде при 90 °С; в — в жидком азоте при -196 °С; г — на воздухе; 1 — минимальная деформация; 2 — максимальная деформация.
Максимальная деформация получается при охлаждении в воде при 20 °С, а минимальная — при охлаждении в жидком азоте и на воздухе.
Коррозия под напряжением – исследование
Одновременно проводили исследования коррозии под напряжением
и межкристаллитной коррозии образцов, закаленных в жидком азоте и в воде при 20 °С. При исследовании коррозии под напряжением образцы в форме петли зажимали в приспособлении и выдерживали в 3%-иом растворе NaCl в течение 3 мес. После таких испытаний трещин на образцах не обнаружено. Признаков межкристаллитной коррозии у плакированных образцов, помещенных на 24 ч в раствор [30 г NaCl+10 мл НС1 (удельный вес 1,19)+ 1 л воды], также не было.
В микроструктуре образцов, закаленных в жидком азоте и в воде, видны равномерно распределенные частицы нерастворившихся вторых фаз, границы зерен α-твердого раствора четко очерчены, однако после закалки в жидком азоте зерна несколько увеличены.
Была проведена закалка в жидком азоте и в воде ребристых панелей из Д16АМ размером 1000×Х700 мм с толщиной стенки 2,5 мм и высотой ребра 25 мм.
После закалки в жидком азоте у панели отсутствовало коробление, а панель, закаленная в воде, имела коробление, трудно исправимое рихтовкой.
Вывод. Закалка тонкостенных деталей из алюминиевых сплавов в жидком азоте при -196 °С позволяет уменьшить коробление до минимума без снижения прочности и коррозионной стойкости. Для деталей сечением до 5 мм из сплава Д16 прочностные характеристики, соответствующие требованиям
ГОСТа, могут быть получены закалкой в жидком азоте.
Е. Г. ИЛЬЮШКО, А. С. БЕДАРЕВ
ISSN 0026-0819. «Металловедение и термическая обработка металлов», № 1. 1968 г.
Литература:
1. Dullberg Е. «The SAE Journal», 1964 v. 72, № 8.
2. «Light Metals and Metal Industry», 1965 v. 28.