Закалка в кипящем слое инструментальных сталей – это процесс, при котором создаются значительные напряжения, вызывающие деформацию, а иногда и трещины, особенно в инструменте сложной конфигурации.
Закалка в кипящем слое (термообработка в кипящем слое)
В последнее время для термической обработки применяют новую охлаждающую среду — кипящий слой [1-3], который обладает высоким коэффициентом (теплообмена (200-1000 ккал/м2·ч·град и более) и дает возможность бесступенчатого регулирования скорости нагрева и охлаждения. Одним из преимуществ кипящего слоя является меньшая деформация деталей при закалке, чем при закалке в других средах [1-3]. Однако сведений по закалке в кипящем слое инструмента пока нет.
Целью настоящей работы было опробование кипящего слоя в качестве закалочной среды для инструмента из сталей Р18 и Х12М.
Схема кипящего слоя
Схема кипящего слоя представлена на рис. 1. В качестве материала кипящего слоя использовали электрокорунд № 12 с размером частиц 0,12-0,16 мм. Режим оптимального псевдоожижения слоя: скорость воздуха 0,22 м/сек, расход воздуха 350 л/мин. Максимальный коэффициент теплообмена слоя при данном режиме псевдоожижения составлял 405,5 ккал/м2·ч·град. Для охлаждения кипящего слоя стенки ванны имеют рубашку, в которой циркулирует холодная вода.
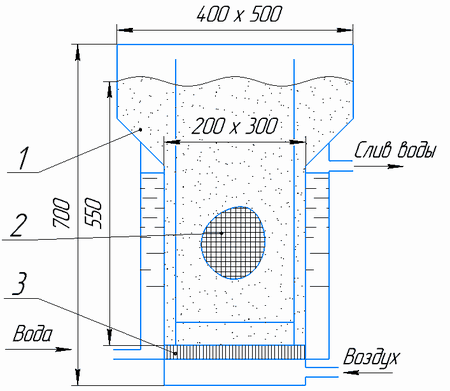
Рис.1. Схема ванны с кипящим слоем:
1 — кипящий слой; 2 — сетчатая корзина; 3 — воздухораспределительная плита.
Охлаждающую способность слоя в сравнении с водой, маслом и расплавленной селитрой (при 300 °С) исследовали на цилиндрическом образце из стали Х18Н9Г1 (рис. 2). Температуру в центре и на поверхности образца измеряли хромель-алюмелевой термопарой. На боковой поверхности образца горячий спай термопары закернивали.
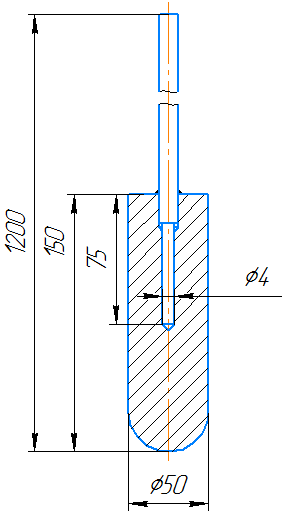
Рис.2. Образец для исследования.
Температуру записывали электронным потенциометром ЭПП-09-ЗМ при скорости движения диаграммы 3600 мм/ч. Образец нагревали в печи Г-30 с защитной атмосферой до 1000 °С.
Из кривых охлаждения образца в различных средах (рис. 3) видно, что интенсивность охлаждения в кипящем слое приближается к интенсивности охлаждения масле.
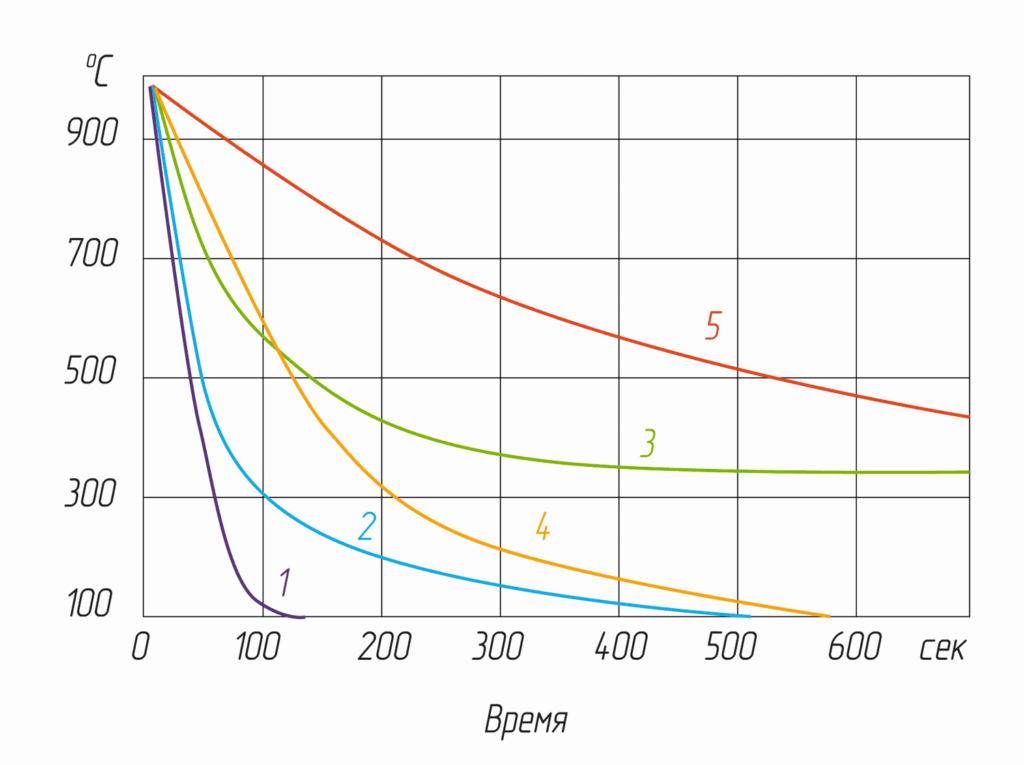
Рис.3. Кривые охлаждения центра образца:
1 — в воде; 2 — в трансформаторном масле; 3 — в селитре (300 °C); 4 — в кипящем слое; 5 — на воздухе.
Температурные перепады по сечению изделий, которые вызывают внутренние напряжения, влияющие на деформацию изделия образование трещин, — существенный фактор при охлаждении металлов и сплавов. Анализ температурных перепадов по сечению образца, охлажденного в разных средах (рис. 4), показал, что при использовании кипящего слоя при всех температурах охлаждения перепад значительно меньше, чем при охлаждении в холодных жидких средах.
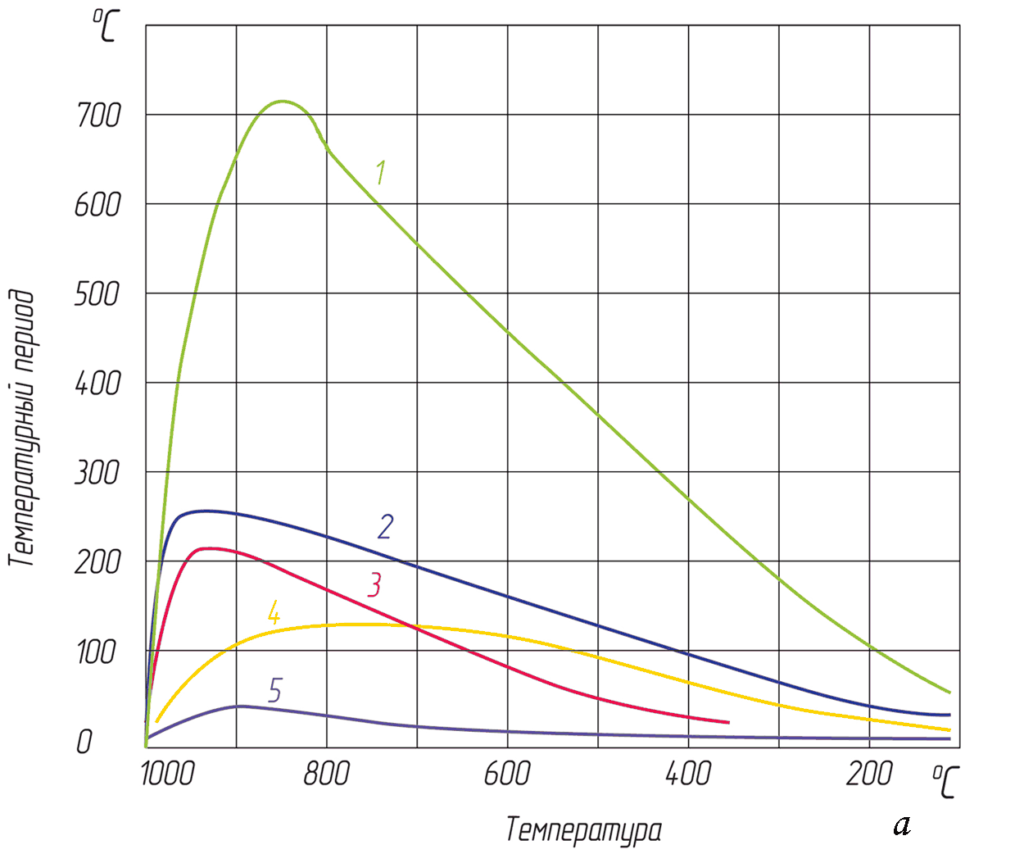
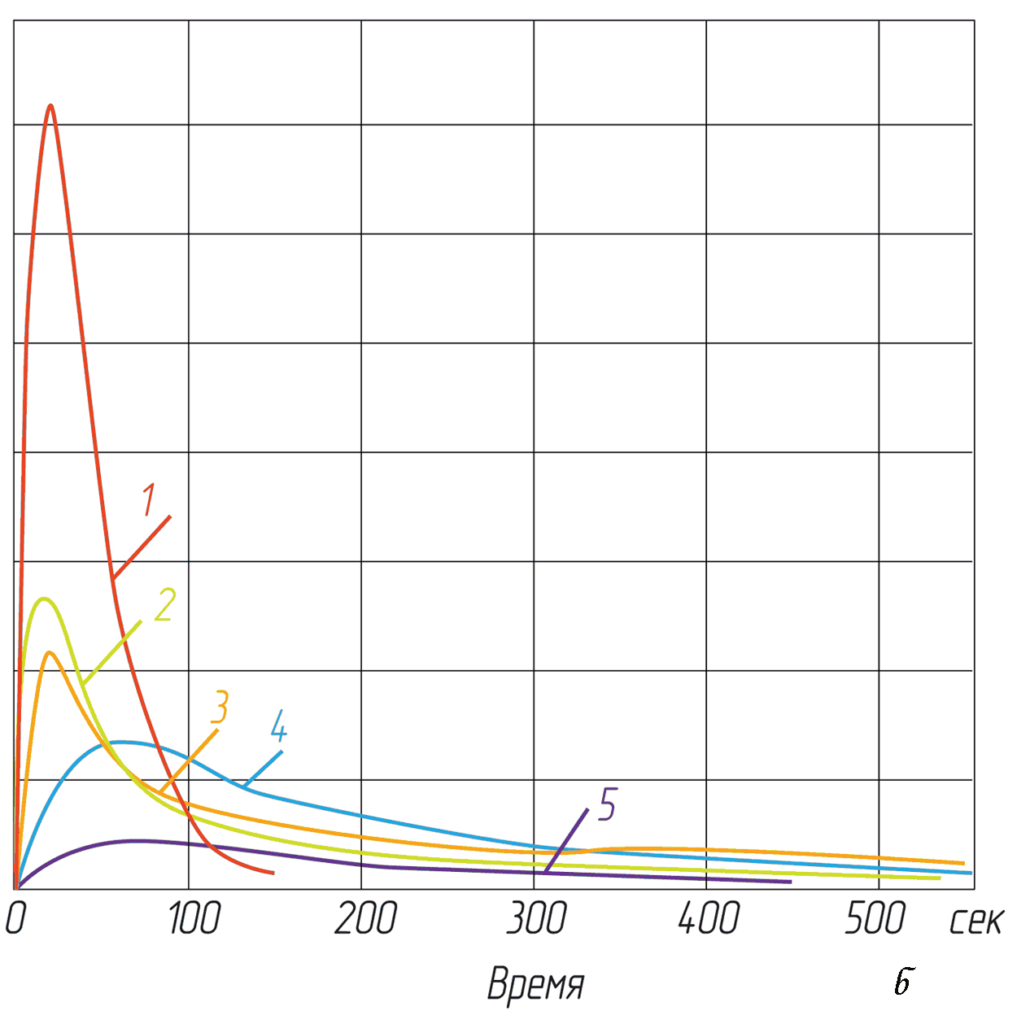
Рис.4. Температурный перепад по сечению образца:
а — в зависимости от температуры центра образца; б — в зависимости от времени охлаждения образца; 1 — охлаждение в воде; 2 — в масле; 3 — в селитре (300 °C); 4 — в кипящем слое; 5 — на воздухе.
Максимум температурного перепада при охлаждении в жидких средах наблюдается в области высоких температур, что особенно опасно для изделий сложной конфигурации.
Таким образом, внутренние напряжения при закалке в кипящем слое должны быть меньше, чем при закалке в жидких средах.
Типы кипящих слоев
Закалку в кипящем слое сталей Р18 и Х12М проводили на образцах диаметром 8 и длиной 150 мм. Для сравнения образцы (типы кипящих слоев) из указанных сталей закаливали также на воздухе, в масле и в расплавленной селитре при 300 °С. Образцы нагревали в лечи Г-30 с защитной атмосферой. Твердость, микроструктуру и деформацию определяли после закалки и после отпуска. За деформацию образцов принимали прогиб в средней части, который замеряли индикатором при установке образцов в центрах. Результаты измерений твердости и деформации приведены в табл. 1. Из приведенных данных видно, что твердость образцов, закаленных в кипящем слое, не отличается от твердости образцов, закаленных в других средах.
Марка стали | Закалка | Отпуск | ||||
Температура в °С | Охлаждающая среда | HRC | Деформация в мм | Температура в °С | HRC | |
Р18 | 1270 | Воздух | 61-61,5 | 0,18-0,28 | 560 (трехкратный) | 61-62,5 |
Масло | 60-61 | 0,30-0,37 | 62-62,5 | |||
Селитра при 300 °С | 59,5-61 | 0,60-0,70 | 62-63,0 | |||
Кипящий слой | 61-61,5 | 0,20-0,28 | 62-63,5 | |||
Х12М | 1120 | Воздух | 46-48 | 0,06-0,13 | 500 (пятикратный) | 60-61,5 |
Масло | 46,5-48 | 0,15-0,20 | 61-61,5 | |||
Селитра при 300 °С | 45,5-47 | 0,05-0,12 | 61-61,5 | |||
Кипящий слой | 47-48 | 0,08-0,10 | 60-61,5 | |||
1000 | Масло | 62-63,5 | 0,07-0,17 | 150 | 62-63,5 | |
Селитра при 300 °С | 62,5-63 | 0,08-0,15 | 62,5-63,5 | |||
Кипящий слой | 62-63 | 0,03-0,07 | 62-63 |
Максимальная деформация образцов из шли Р18 наблюдается при закалке в селитре при 300 °С, что по-видимому, связано с перераспределением углерода в аустените при изотермическом превращении его в мартенсит. Образцы, закаленные в кипящем слое и на воздухе, имеют меньшую деформацию, чем после закалки в масле. Образцы из стали Х12М, закаленные с 1120 и 1000 °С, также имеют меньшую деформацию после охлаждения в кипящем слое и на воздухе, чем после закалки в масле.
После отпуска закаленных образцов деформация во всех случаях не изменялась. В микроструктуре закаленных и отпущенных образцов не было различия.
Нагрев в кипящем слое
Нагрев в кипящем слое образцов из стали Р18, которые испытывали на красностойкость после нагрева при 600, 625, 650 и 675 °С в течение 4 ч. Результаты испытаний, приведенные в табл. 2, показывают, что красностойкость образцов, закаленных в кипящем слое, масле и селитре, одинакова, а образцов, закаленных на воздухе, — ниже.
Охлаждающая среда | Твердость после термической обработки HRC | HRC после нагрева 4 ч при температуре в °С | |||
600 | 625 | 650 | 675 | ||
Кипящий слой | 62..63,5 | 60..61 | 58,5..59 | 57..58 | 47,5..48 |
Масло | 62..62,5 | 60..61 | 58..59 | 56..57 | 47..48 |
Селитра при 300 °C | 62..63 | 60..61 | 58..59 | 57..58 | 46..48 |
Воздух | 61,5..62 | 58..59 | 56..57 | 49..50 | 45,5..46 |
Испытания на прокаливаемость сталей Р18 и Х12М проводили на образцах сечением 25×25 мм и длиной 150 мм по методу Гудцова [4]. Образцы прокаливались на всю длину при закалке в масле и в кипящем слое.
Опробование закалки в кипящем слое одновременно с закалкой в масле и селитре различных видов инструмента из сталей Р18, Р9, Р18К5Ф2, Х12М и Х12Ф1 (сверла, протяжки, фрезы, метчики, резцы и др.) показало, что деформация инструмента, закаленного в кипящем слое, значительно меньше, чем после закалки в других средах при одинаковой твердости.
Инструмент под закалку нагревали в печи Г-30 с защитной атмосферой и в хлор-бариевой ванне. Инструмент, закаленный в кипящем слое, имел чистую поверхность. При использовании хлор-бариевой ванны наблюдалось налипание на поверхности инструмента частиц корунда, которые не оказывали существенного влияния на процесс охлаждения. Налипший слой частиц толщиной 0,2-0,3 мм легко удалялся протиркой или опескоструиванием после промывки инструмента от соли.
Эксплуатация инструмента, закаленного в обычных средах и в кипящем слое, показала одинаковую его работоспособность.
Выводы.
1. Охлаждающая способность кипящего слоя приближается к охлаждающей способности масла.
2. Температурный перепад по сечению охлаждаемых в кипящем слое деталей и их деформация значительно меньше, чем использовании обычных жидких сред.
3. Кипящий слой может быть успешной использован в качестве закалочной среды для высоколегированных инструментальных сталей.
В. П. КУРБАТОВ, В. И. МУРАВЬЕВ
ISSN 0026-0819. «Металловедение и термическая обработка металлов», № 2. 1970 г.
Список литературы:
1. Варыгин Н. Н. «МиТОМ», 1961 № 6.
2. Вennet С., Jung С. «Metall Progress», 1961, v. 79, № 4.
3. Вrittain C. and others. «Metall Industry», 1963, v. 103, № 4.
4. Справочник «Металловедение и термическая обработка». М.: Металлургиздат, 1956.